An engineering economic analysis may involve many types of costs. Here is a list of cost types, including definitions and examples.
A fixed cost is constant, independent of the output or activity level. The annual cost of property taxes for a production facility is a fixed cost, independent of the production level and number of employees.
A variable cost does depend on the output or activity level. The raw material cost for a production facility is a variable cost because it varies directly with the level of production.
The total cost to provide a product or service over some period of time or production volume is the total fixed cost plus the total variable cost, where:
Total variable cost = (Variable cost per unit) (Total number of units)
A marginal cost is the variable cost associated with one additional unit of output or activity. A direct labor marginal cost of $2.50 to produce one additional production unit is an example marginal cost.
The average cost is the total cost of an output or activity divided by the total output or activity in units. If the total direct cost of producing 400,000 is $3.2 million, then the average total direct cost per unit is $8.00.
The breakeven point is the output level at which total revenue is equal to total cost. It can be calculated as follows:
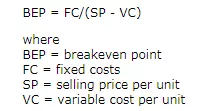
A sunk cost is a past cost that cannot be changed and is therefore irrelevant in engineering economic analysis. One exception is that the cost basis of an asset installed in the past will likely affect the depreciation schedule that is part of an after-tax economic analysis. Although depreciation is not a cash flow, it does affect income tax cash flow. Three years ago, an engineering student purchased a notebook PC for $2,800. The student now wishes to sell the computer. The $2,800 initial cost is an irrelevant, sunk cost that should play no part in how the student establishes the minimum selling price for the PC.
An opportunity cost is the cost associated with an opportunity that is declined. It represents the benefit that would have been received if the opportunity were accepted. Suppose a product distributor decides to construct a new distribution center instead of leasing a building. Leasing a building immediately would have resulted in a $12,000 product distribution cost savings during the next 6 months while the new warehouse is being constructed. By forgoing the warehouse leasing alternative, the distributor experiences an opportunity cost of $12,000.
A recurring cost is one that occurs at regular intervals and is anticipated. The cost to provide electricity to a production facility is a recurring cost.
A nonrecurring cost is one that occurs at irregular intervals and is not generally anticipated. The cost to replace a company vehicle damaged beyond repair in an accident is a nonrecurring cost.
An incremental cost represents the difference between some type of cost for two alternatives. Suppose that A and B are mutually exclusive investment alternatives. If A has an initial cost of $10,000 while B has an initial cost of $12,000, the incremental initial cost of (B – A) is $2,000. In engineering economic analysis we focus on the differences among alternatives, thus incremental costs play a significant role in such analyses.
A cash cost is a cash transaction, or cash flow. If a company purchases an asset, it realizes a cash cost.
A book cost is not a cash flow, but it is an accounting entry that represents some change in value. When a company records a depreciation charge of $4 million in a tax year, no money changes hands. However, the company is saying in effect that the market value of its physical, depreciable assets has decreased by $4 million during the year.
Life-cycle costs refer to costs that occur over the various phases of a product or service life cycle, from needs assessment through design, production, and operation to decline and retirement.
Comments are closed.